Introduction
Amino resins are thermosetting polymers produced from a reaction between aldehyde and compounds containing amino (NH2) group. More than 80% of amino resins are created from urea-formaldehyde (U/F) and the rest constituents are melamine-formaldehyde (M/F), Benzoguanamine, and other amino resins. The first commercially important amino resin was produced in 1920, or almost 20 years after the introduction of phenol-formaldehyde resins.
Some advantages of amino resin compounds are as follows: unlimited colorability with dyes and pigments, excellent solvent resistance, hardness and resistance against abrasion, and good thermal resistance.
The increasing trend of consuming amino resins during the recent years is shown in the following chart. The global market value of amino resins is expected to increase to approximately 31.33 billion dollars in 2027, with the annual grow rate of 8.9% from 2020 to 2027. Demand for amino resins is ever increasing due to their excellent properties and wide applications in construction, automotive industry and other sectors. Thus, demand for their consumption will be increasingly in future.
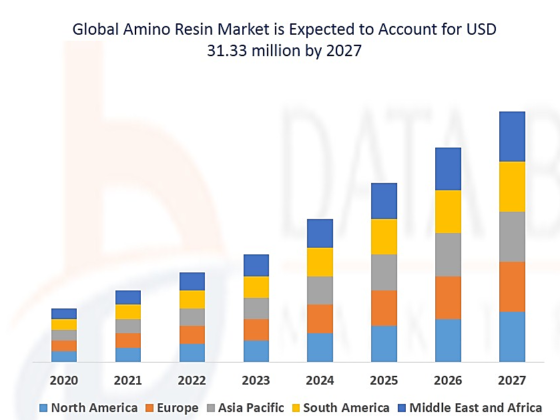
Most amino resins are formed from a reaction between formaldehyde and either urea, melamine, or benzoguanamine. The following figures show three monomers: urea, melamine, and benzoguanamine.
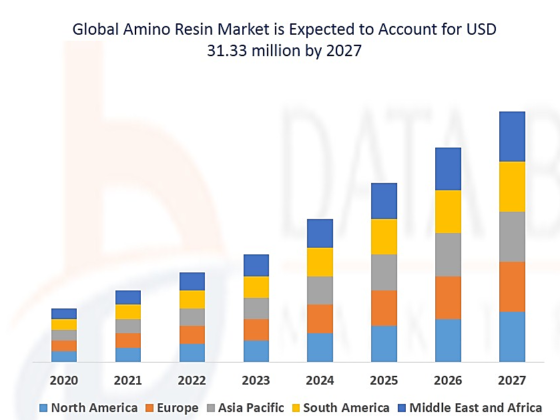
The use of benzoguanamine is less frequent than urea and melamine in amino resins. Benzoguanamine provides better adhesiveness than melamine and so it has more application in surface coatings. However, its poor UV resistance compared to melamine limits its application. Moreover, dramatic increase of benzoguanamine price compared to that of melamine has decreased its consumption as a commercial product during the recent years.
Synthesis of Amino Resins
In order to make methylol compounds, we first add formaldehyde to amine groups.

Then, methylol compounds through a condensation reaction convert to polymers. These reactions may happen either between two methylol groups or between a methylol group and active hydrogen atoms.

Products of this reaction have properties such as limited water solubility, insolvability in solvents, and instability. In order to be used in surface coatings, these polymers are modified via reacting with alcohols. Modified polymers have improved stability, modified solubility, and increased compatibility with other polymeric compounds. Thus, various types of alcohols can be used depending on our purpose.

Properties and Applications of Amino Resins
In the early 1920s, experimentation with urea-formaldehyde resins in Germany and Austria led to the discovery of beautiful transparent sheets, and it was proposed that this new synthetic material might be used to manufacture synthetic glass. However, the lack of sufficient water resistance prevented its commercialization. While melamine-formaldehyde resins have better water resistance, the market for synthetic glass was taken over by new thermoplastic materials such as polystyrene and poly (methyl methacrylate).
Amino resins have more transparency and hardness (tensile resistance) than phenol derivatives. However, their impact resistance and heat resistance are less. In general, melamine-formaldehyde resins have better properties than urea-formaldehyde resins. Melamine-formaldehyde resins are more expensive than urea resins, and consequently, they are preferred in higher functional applications. In addition, the exceptional stability of the symmetrical triazine ring made the products of this resin resistant to chemical changes. Melamine resins have good resistance against heat and moisture and better hardness than urea resins.


The applications of amino resins are categorized into three general classes. First, there are materials in which amino resins are the main ingredients; adhesives, laminating resins, and molding compounds are some of the important examples. Molding compounds based on amino resins are used for parts in electrical devices, bottle and jar caps, plastic dinnerware, and buttons.
The second class contains the amino resins, which are used as additives. For example, adding a small amount of amino resin to textile fabric enhances the after-wash durability of clothes. Automotive tires are strengthened by amino resins, which improve the adhesion of tubber to tire cord. An amino resin coating on papers can improve the strength of paper even when it is wet.
The third class of applications include coating applications in which amino resins are used as curing agents for other resins such as alkyd resins and acrylic polymers. These applications are highly diverse depending on the type of amine and alkyl in use, the degree of polymerization, and eventually, formulation design.
- Molding compounds and powder amino resins
Molding was the first great application for amino resins. Molding compounds are more complex compared to adhesives or laminating resins. A simple amino-resin molding compound may be made by combining melamine with 37% formalin in the ratio of 2 mol formaldehyde/1 mol melamine at neutral or even slightly alkaline pH and a temperature of 60 °C.To make the molding materials, cellulose and melamine resin are combined in a ball mill with a catalyst, stabilizer, colorants, and lubricants. The materials must be ground for several hours to achieve the uniform dispersion and the desired decorative shape in the mold. Using a resin made with 1.3 to 1.5 mol of formaldehyde/1.0 mol of urea is a suitable combination for molding. Urea-resin molding compounds are now widely used in wiring devices and electrical surfaces.

- Amino Resins in Coating Industry
Cured amino resins are very brittle and cannot be used alone as surface coatings for metal or wood substrates. However, a wide range of acceptable properties can be achieved in combination with other film formers (alkyds, polyesters, acrylics, and epoxies). These combined coating materials cure rapidly at slightly high temperatures, making them suitable for industrial purposes. In coating applications, all amino resins are usually alkylated to some extent to provide compatibility with other film formers used in the coating formulation. Amino resins used in the coatings industry vary not only in the type of amine (melamine, urea, benzoguanamine, and glycoluril) used, but also in the molar content of formaldehyde, and the type and concentration of alkylation alcohol (n-butanol, isobutyl alcohol, and methanol).
- Amino resins and improving textile properties
Most amino resins used commercially for improving the properties of textile fabrics are methylated derivatives of urea or melamine. While these products are usually monomeric, they may contain some polymeric by-products. Amino resins react with cellulosic fibers and change their physical properties. This changes the hardness or flexibility of the fiber.
Resitan Co. manufactures several alkylated amino resins as the curing agents for other resins (e.g., alkyds, polyesters, acrylics and epoxies). Two types of melamine-formaldehyde resin MF-121 and MF-122, two types of benzoguanamine-formaldehyde resin BF-181 and BF-182, and two types of urea-formaldehyde resins UF-151 and UF-152 are among the applicable resins in the paint and varnish industries.